New technologies
New technologies
Hot Isostatic Pressing (HIP) + forming
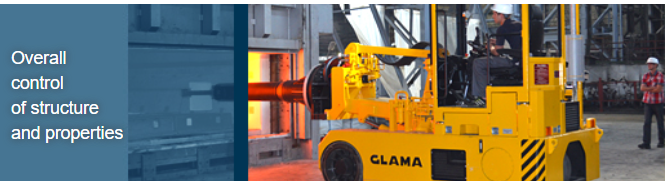
Hot Isostatic Pressing (HIP) + forming is a rare and advanced technology of manufacturing of semi-finished products; this technology allows us to achieve products with higher performance level.
Our mission is to provide the manufacturers the products of highest performance level for improving the performance of the final products.
The main point of this technology is the sequential integration of hot isostatic pressing (HIP) of granules and forming.
Using HIP technology DMK granule metallurgy workshop produces the granules of the specified fraction composition from heat-resistant nickel- and titanium-based alloys in the protective environment.
Then, at forming stage, the semi-finished products manufactured from granules are heated up to very high temperatures (max 1250°C) with the set accuracy (± 7°C). Forging tool is heated directly in the press and the metal is wrought at the specified speed.
Parts resulted from this pattern contains the system of higher performance and indicators compared to the traditional HIP technology.
In particular, this technology provides the opportunity to produce components with individual sets of characteristics in different parts (hub, web, and rim) depending on operating conditions of the part. It is possible to produce disks with the embedded elements through HIP + forming technology including the usage of the granules of different fraction composition, chemical composition in different parts of the disks so as to achieve the individual characteristics through the gradient structure provided in the cross section of the part.
Granules of titanium-based alloys
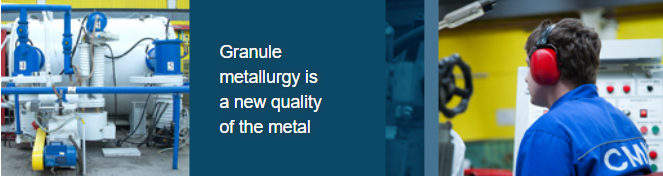
DMK Granule Metallurgy Facility produces the granules of titanium-based alloys.
Titanium granules are the parent material for production of parts for different purposes using the technology of selective laser induced synthesis. This technology is increasingly applied in different fields.
It is possible to use granules of titanium-based alloys for production of parts with structural application through HIP or HIP + forming.
Such semi-finished products have the significant advantages over forged parts. In particular, parts produced from granules have no part size anisotropy, they have uniform isotropic structure so as to provide the stable set of properties in all sampling trends and part elements.
Research and production cooperation
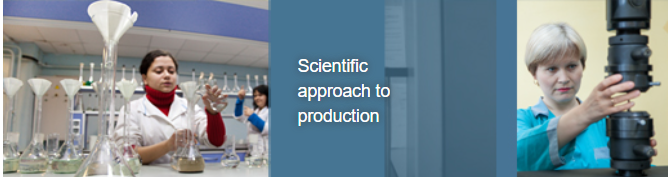
DMK closely cooperates with industrial scientific institutions.
Within this ciiperation the research scientific work is provided, pilot batches are produced, and new materials and processes in special metallurgy for serial production are introduced to ensure the improvement of the existing equipment as well as manufacturing of equipment of new generation.